Service Management Built for Construction Plant & Heavy Equipment

The #1 choice for thousands of industry leaders
Keep Heavy Machinery Running Smoothly
Prevent Breakdowns & Delays
Unexpected failures on-site lead to project delays and high repair costs. Service Geeni keeps machinery running with proactive maintenance and asset tracking.
- Automate servicing schedules to ensure equipment is maintained at the right intervals.
- Detect issues early with performance insights, reducing costly emergency repairs.
- Keep projects on track by preventing equipment downtime and last-minute service disruptions.


Improve Engineer Efficiency
Construction sites demand fast response times and skilled engineers. Service Geeni optimises scheduling and job tracking to ensure smooth operations.
- Assign jobs based on availability, skill set, and proximity to improve first-time fix rates.
- Enable real-time job tracking to ensure service teams are working efficiently.
- Reduce admin work with digital job sheets and automated reporting.
Gain Full Asset Visibility
Managing heavy machinery and site equipment across multiple locations is complex. Service Geeni's software provides a single platform for complete asset management.
- Track service history and usage to optimise maintenance planning.
- Monitor equipment across multiple sites for better resource allocation.
- Reduce unplanned servicing with predictive insights based on asset performance.

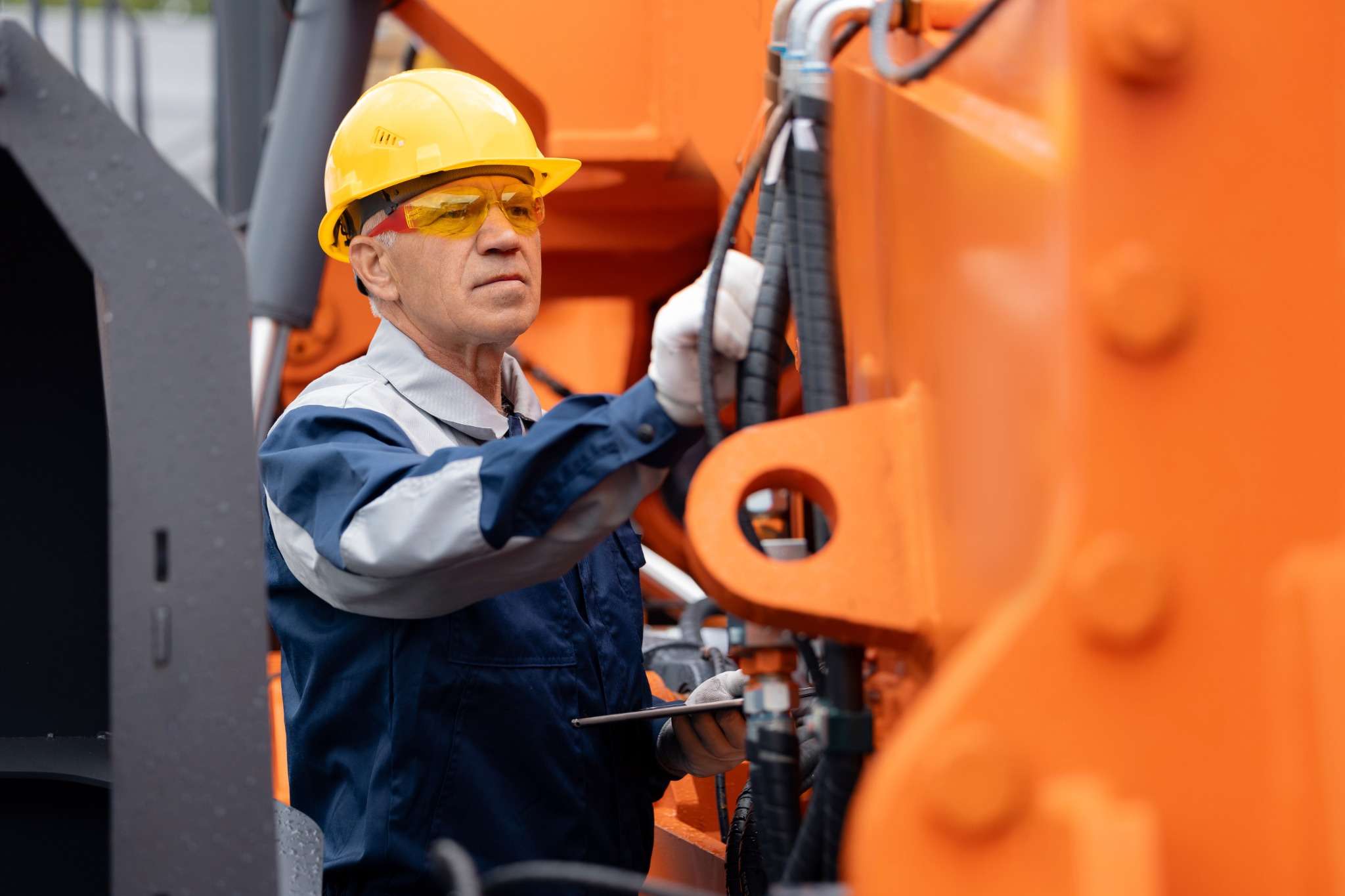
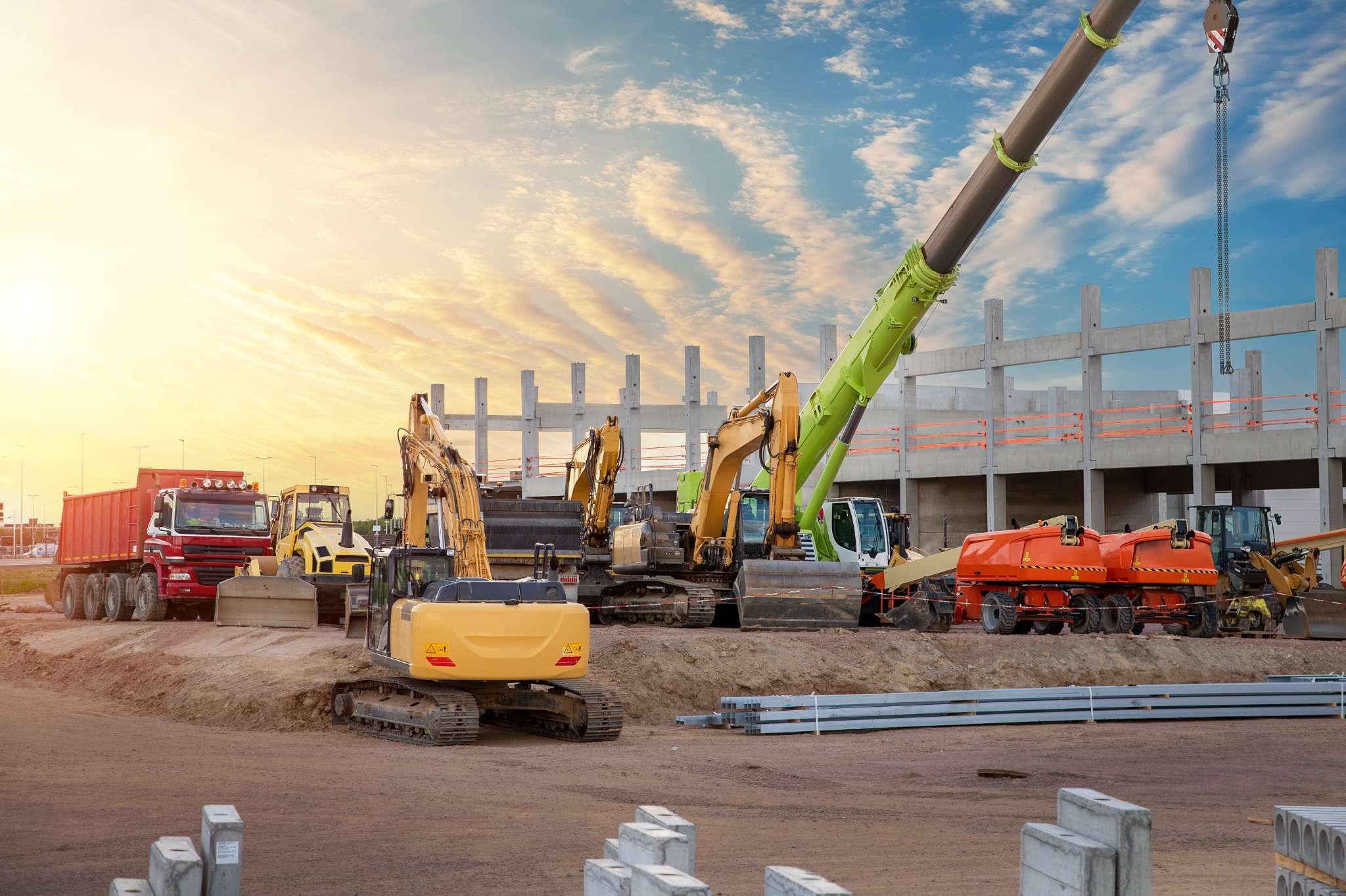
Built for the Demands of Construction & Heavy Equipment
Real Businesses, Real Results
.avif)
You have questions,
we have answers
Service Geeni is designed to handle the complex demands of aviation and ground support equipment (GSE) maintenance, and offers a whole lot more than many aircraft maintenance software providers can. It automates servicing schedules, tracks asset performance in real time, and optimises engineer dispatch to prevent downtime.
Our service management software ensures compliance with safety regulations, keeps essential equipment like aircraft tugs, GPUs, and de-icing rigs operational, and provides full visibility over service history and parts availability. Whether managing assets across terminals or coordinating urgent repairs, Service Geeni helps aviation businesses keep operations running smoothly and on schedule.
Unplanned failures of ground power units (GPUs), aircraft tugs, and de-icing rigs can cause severe flight delays. With features comparable to even the most specialist aviation maintenance software, Service Geeni automates servicing schedules based on usage hours and condition monitoring, ensuring GSE stays operational when needed.
Yes, our asset tracking system provides real-time location visibility for mobile GSE like belt loaders, refuelers, and baggage tugs. This prevents misplaced equipment and ensures efficient allocation across airport zones.
With real-time fault logging via the mobile app, engineers can report issues immediately. Service Geeni software then assigns jobs based on proximity and skill set, ensuring quick dispatch to fix aircraft stairs, tow tractors, or hydraulic lifts - key capabilities in aviation maintenance software.
Yes, our stock and parts management feature ensures that high-usage components - like hydraulic hoses for scissor lifts, filters for air start units, or brake pads for pushback tugs - are always in stock. Automated reordering prevents delays due to missing parts.
Yes, our service management software helps maintain compliance with aviation safety regulations by tracking service records, inspection reports, and preventative maintenance for assets like jet bridges, fuel hydrant carts, and lavatory service trucks.
Yes, our reporting tools provide detailed insights into fuel consumption, servicing expenses, and asset lifecycle costs for equipment like refuelling trucks and air start units, helping airlines and ground crews reduce costs and improve efficiency.
For companies renting out GSE, Service Geeni tracks rental agreements, service schedules, and condition history for leased equipment such as mobile passenger stairs, loaders, and forklifts. This ensures proper GSE and aviation maintenance and compliance with lease terms.
You have questions,
we have answers
Service Geeni is built to keep forklifts, conveyors, and other material handling equipment running smoothly with:
Asset-Focused Maintenance – Tracks each asset’s history, performance, and depreciation.
Automated PPM Scheduling – Reduces downtime and ensures LOLER & PUWER compliance.
Fast Breakdown Response – Auto-assigns the nearest qualified engineer with the right parts.
Stock & Parts Tracking – Prevents delays with automated reordering and van stock sync.
Compliance & Reporting – Digitally logs service records and inspections for safety audits.
Multi-Site Visibility – Manages assets across warehouses, depots, or rental fleets.
Hire & Rental Support – Tracks service history to keep rental equipment in peak condition.
By reducing downtime and improving efficiency, Service Geeni software keeps material handling operations moving.
Yes, our material handling management software tracks a wide range of equipment, including forklifts, conveyors, cranes, trucks, and other industrial machinery. Each asset is monitored individually, allowing for precise performance tracking, maintenance scheduling, and cost analysis.
Service Geeni automates maintenance scheduling, tracks asset usage in real-time, and alerts engineers to potential faults before they escalate. By ensuring preventative maintenance is completed on time and automating fault reporting, our material handling software helps minimise unexpected breakdowns and keeps operations running smoothly.
When a conveyor, lift truck, or pallet mover breaks down, every minute of downtime impacts productivity. Service Geeni automatically assigns the nearest available engineer with the right skills and parts to the job, reducing response times and getting equipment back in service faster.
High-use assets in warehouses and distribution centers require frequent servicing. Service Geeni tracks asset usage in real-time and can schedule maintenance based on actual workload, rather than just fixed intervals. This prevents overuse-related failures while avoiding unnecessary servicing and engineer costs.
Absolutely. Service Geeni includes digital forms and checklists for safety inspections, risk assessments, and compliance reporting. Engineers can complete these checks on-site via the mobile app, ensuring that all equipment remains compliant with industry regulations.
Yes, for hire and rental companies, Service Geeni tracks equipment usage, service history, and rental periods. It helps ensure that machines are returned in working order, with automated reminders for maintenance between hire periods to avoid unexpected breakdowns.
Yes, Service Geeni integrates with various third-party systems, including accounting software, CRM tools, and ERP platforms, ensuring seamless data flow across your entire business.
You have questions we have answers
Service Geeni’s equipment rental software automatically logs maintenance schedules based on manufacturer recommendations, usage hours, or rental history. It then sends reminders to your team when servicing or inspections are due, ensuring nothing gets overlooked.
Service Geeni’s equipment rental software automatically logs maintenance schedules based on manufacturer recommendations, usage hours, or rental history. It then sends reminders to your team when servicing or inspections are due, ensuring nothing gets overlooked.
Service Geeni’s equipment rental software automatically logs maintenance schedules based on manufacturer recommendations, usage hours, or rental history. It then sends reminders to your team when servicing or inspections are due, ensuring nothing gets overlooked.
Service Geeni’s equipment rental software automatically logs maintenance schedules based on manufacturer recommendations, usage hours, or rental history. It then sends reminders to your team when servicing or inspections are due, ensuring nothing gets overlooked.
Service Geeni’s equipment rental software automatically logs maintenance schedules based on manufacturer recommendations, usage hours, or rental history. It then sends reminders to your team when servicing or inspections are due, ensuring nothing gets overlooked.
Service Geeni’s equipment rental software automatically logs maintenance schedules based on manufacturer recommendations, usage hours, or rental history. It then sends reminders to your team when servicing or inspections are due, ensuring nothing gets overlooked.
Yes, our software tracks your equipment usage through meter readings, GPS tracking, and rental data. It can trigger maintenance tasks based on actual usage (e.g., hours operated or distance travelled) rather than just fixed calendar dates, helping you to keep on top of important maintenance tasks at the ideal times to keep your machinery running and customers happy!
Yes, your assets are at the forefront of our software’s capabilities. What does this mean for you as a hire company? It means you have access to past maintenance, repairs, parts replacements, and servicing logs for every single asset within your business. This information ensures you can stay compliant, manage warranties, and make informed decisions about equipment repairs or replacements.
Absolutely. The system can schedule safety inspections, generate compliance reports, and ensure that all equipment meets industry regulations. It also provides digital checklists for pre-hire inspections to confirm that machinery is safe and ready for use.
By proactively scheduling maintenance and alerting teams to upcoming service needs, the software helps prevent unexpected breakdowns. Real-time tracking of faults and repairs ensures that issues are addressed quickly, reducing downtime and maximising equipment availability. This benefits both you and your customers, keeping your revenue coming in and ensuring your equipment is available to customers as and when they need it.
You have questions,
we have answers
Combining essential features of catering equipment software with advanced service management tools for predictive maintenance, asset performance tracking, and compliance management, Service Geeni is ideal for catering and refrigeration maintenance. It automates maintenance schedules, reduces downtime, and ensures compliance with F-Gas regulations.
With features like real-time fault logging, asset performance tracking, and efficient engineer scheduling, it helps keep kitchen and foodservice equipment like ovens and refrigerators operational, minimising delays and food waste.
Field service management software automates maintenance schedules for catering equipment like ovens, fryers, and coffee machines, ensuring regular servicing and reducing the risk of unexpected breakdowns. This proactive approach helps keep your kitchen running smoothly, reducing downtime during busy service hours.
Yes, Service Geeni tracks all required safety checks and service intervals, including inspections for food safety compliance. Whether it's ensuring your ovens meet local regulations or tracking calibration for food prep equipment, our software helps maintain compliance with industry standards.
Our software features enable real-time tracking of equipment performance, ensuring you can identify and address any faults before they disrupt operations. Whether it's an oven that's overdue for service or a fryer showing signs of wear, you'll get alerts to take action and avoid costly breakdowns.
Our software automates job scheduling based on the priority and availability of engineers, matching them with specific tasks like repairing dishwashers, ovens, or refrigerators. This ensures fast response times and reduces delays, so you don’t experience interruptions during peak hours.
Service Geeni allows engineers to log faults instantly via a mobile app, providing real-time visibility into equipment performance. You can access detailed service history for all equipment, from coffee machines to ovens, helping you identify recurring issues and optimise future maintenance schedules.
Yes, our service management software includes F-Gas tracking for refrigeration systems. It automatically monitors refrigerant usage, tracks leak checks, and generates audit-ready reports, ensuring your catering equipment stays compliant with regulations while reducing environmental impact.
For catering businesses with multiple sites, Service Geeni provides real-time asset tracking and centralised maintenance management. You can monitor equipment status, schedule service tasks, and track performance trends across all locations, ensuring consistency and preventing downtime at each site.
You have questions,
we have answers
Service Geeni is designed specifically for managing the complexities of heavy equipment maintenance, including the management of construction equipment. It provides full asset tracking, automated maintenance scheduling, and real-time job management, helping businesses prevent breakdowns, reduce downtime, and improve overall efficiency.
With features like engineer dispatch optimisation, predictive maintenance insights, and stock control, our software ensures that construction equipment stays operational, projects remain on schedule, and engineers are efficient.
Construction projects depend on reliable equipment. Service Geeni automates servicing schedules based on usage hours and condition tracking, flags potential faults before they cause failures, and ensures critical spare parts are always available, preventing costly downtime.
Yes, our asset tracking system allows you to monitor equipment across multiple locations, ensuring you always know where your machines are, who’s using them, and when they’re due for maintenance.
Engineers receive real-time job updates, access to digital service histories, and parts availability information on-site, ensuring faster repairs and fewer delays. The engineer mobile app allows instant job reporting, eliminating paperwork and speeding up service completion.
Yes, Service Geeni supports both owned and plant hire equipment. You can track rental agreements, servicing schedules, and usage logs to avoid unnecessary costs and ensure compliance with hire contracts.
Yes, our stock and parts management system ensures that high-use components - such as hydraulic filters, tracks, and engine parts - are always in stock. Automatic reordering prevents delays caused by missing parts, keeping repairs on schedule.
By optimising job scheduling, tracking equipment usage, and automating maintenance, Service Geeni reduces unplanned downtime, prevents project delays, and ensures engineers are dispatched efficiently - keeping operations running smoothly.
Yes, Service Geeni provides detailed reporting on fuel consumption, servicing expenses, and asset depreciation, helping construction firms manage budgets, reduce waste, and improve cost-efficiency.
You have questions,
we have answers
Service Geeni software is perfect for HVAC maintenance because it automates service scheduling, tracks F-Gas compliance, and monitors asset performance in real time. It optimises job assignments for engineers based on priority and expertise, improving first-time fix rates and reducing downtime.
Ultimately, the platform streamlines maintenance workflows, ensuring HVAC systems stay operational and compliant, while enhancing efficiency and service speed.
Service Geeni automates preventative maintenance schedules for HVAC systems, ensuring timely servicing that extends the lifespan of equipment. By monitoring performance trends and real-time fault reports, it helps detect issues before they lead to costly breakdowns, reducing emergency callouts and downtime.
Service Geeni's HVAC software integrates stock and parts management with job scheduling, ensuring HVAC engineers are equipped with the correct parts before they head to the site. Real-time tracking of parts inventory ensures that engineers are alerted to low stock levels, preventing delays in completing jobs due to missing parts.
Service Geeni's HVAC service software streamline engineer workflows by providing instant access to job details, service history, and inventory information through a mobile app. The software optimises job scheduling based on location, expertise, and urgency, improving first-time fix rates and overall efficiency.
Yes, our service management software automates F-Gas tracking and reporting to help HVAC service providers meet regulatory requirements. It logs refrigerant usage, schedules leak detection checks, and generates audit-ready reports, reducing the administrative burden and ensuring compliance with F-Gas regulations.
With real-time job tracking and instant access to service history, parts inventory, and fault reports, our HVAC software helps engineers respond quickly to urgent service requests. The platform also optimises engineer dispatch based on location and skill set, ensuring the right technician is assigned to each job for faster resolution.
Yes, Service Geeni provides real-time asset tracking across multiple sites. Whether you manage HVAC systems in commercial buildings, industrial facilities, or residential units, our software helps monitor equipment performance, schedule maintenance, and track service histories in one centralised platform.
You have questions we have answers
Service Geeni's industrial and manufacturing maintenance software optimises servicing and repairs for CNC machines, compressors, generators, and more with automated scheduling, predictive servicing, and real-time tracking.
It helps prevent breakdowns, minimise downtime, and ensure critical parts are always in stock. With integrated job scheduling, compliance tracking, and reporting, businesses can streamline maintenance and keep operations running smoothly.
Our service management software for industrial and manufacturing automates maintenance schedules, detects early signs of equipment failure, and ensures engineers are dispatched promptly. By tracking asset performance in real-time, manufacturers can prevent costly breakdowns and production delays.
Yes, Service Geeni enables planned preventative maintenance to be scheduled outside peak production hours. For example, a manufacturing plant can service its compressors and generators during shift changes to prevent disruption while keeping operations efficient.
Yes, our asset and equipment tracking system allows manufacturers to monitor machinery across multiple sites, ensuring full visibility over servicing history, performance data, and maintenance schedules.
Running out of essential parts can lead to prolonged downtime. Service Geeni’s stock and parts management feature ensures that critical components -such as CNC tool heads, compressor filters, or hydraulic seals for waste compactors - are always available by automating stock tracking and reordering alerts.
Yes, instead of waiting for failures, Service Geeni uses real-time monitoring and trend analysis to predict maintenance needs. For example, if a generator starts running at reduced efficiency, the system alerts engineers before a complete failure occurs, reducing unexpected disruptions.
Service Geeni keeps detailed digital records of all inspections, servicing, and maintenance tasks, ensuring compliance with industry regulations. Whether it’s LOLER inspections for lifting equipment or servicing logs for waste processing machines, businesses can automate scheduling and keep audit-ready records.
Yes, our reporting and business intelligence feature helps track servicing costs, downtime expenses, and asset efficiency. For example, manufacturers can compare the maintenance costs of multiple CNC machines to decide whether to repair or replace underperforming equipment.
Yes, many businesses rely on third-party providers for specialist maintenance, such as contracted servicing for compressors or waste processing units. Our software allows businesses to assign, track, and verify outsourced maintenance jobs, ensuring all servicing is logged and performance is monitored.
You have questions,
we have answers
Service Geeni is ideal for lifting equipment maintenance due to its automated maintenance scheduling, full asset visibility, and compliance tracking. It ensures equipment is serviced on time, including LOLER inspections, to meet safety regulations and reduce downtime. Our platform provides real-time updates, allowing engineers to quickly access service histories and perform efficient repairs, improving both compliance and operational efficiency.
Staying compliant with safety regulations is critical for lifting equipment, and keeping on top of this will also help extend its lifespan. Service Geeni's service management software helps you stay on top of LOLER inspections (thorough examinations), ensuring all equipment is regularly inspected, certified, and compliant with legal standards. This reduces the risk of penalties and ensures the safety of your team and equipment.
Yes, Service Geeni’s asset tracking capabilities allow you to monitor lifting equipment across multiple job sites. You’ll always know the location, service history, and condition of each piece of equipment, helping you optimise fleet usage and minimise downtime.
Service Geeni reduces downtime through proactive maintenance scheduling, automated reminders, and real-time fault logging. The software identifies issues before they cause failures and helps ensure that parts and engineers are available when needed, minimising delays.
Yes, Service Geeni is well-suited for hire and rental companies. You can track rental agreements, monitor equipment usage, and ensure timely servicing to avoid unplanned downtime and keep rental fleets operational. The software also helps ensure compliance with safety regulations and track assets in real time.
Service Geeni’s stock and parts management system ensures critical parts for lifting equipment, like hydraulics and safety components, are always in stock. The system automatically generates reordering alerts, helping you avoid delays and ensuring engineers have the right parts on hand.
You have questions,
we have answers
Service Geeni is a great fit for medical equipment maintenance companies because it makes it easy to track service history, parts used, and maintenance schedules. It helps you stay compliant with regulations, like FDA standards, and keeps all your documentation in order for audits and inspections. The platform streamlines maintenance workflows, helping medical organisations stay on top of things while keeping equipment running smoothly and efficiently.
By automating maintenance schedules and enabling real-time tracking of device performance, Service Geeni helps detect potential issues before they cause failures. Engineers can log faults instantly, monitor recurring issues, and take preventative action to ensure medical devices remain operational.
Service Geeni prioritises urgent repairs by assigning the closest available engineer with the right expertise. Real-time job tracking and instant notifications help speed up response times, ensuring critical medical equipment is repaired quickly to avoid disruption to patient care.
Absolutely. The software enables service teams to schedule PPM tasks based on usage, manufacturer guidelines, and regulatory requirements. This proactive approach helps extend the lifespan of critical medical devices and reduces the risk of sudden failures.
Yes, Service Geeni automates calibration schedules and logs all performance testing results digitally. It provides a complete service history for each device, ensuring accurate tracking of test results, certifications, and adjustments. Engineers can easily access past calibration data to ensure compliance with performance standards.
Service Geeni optimises engineer scheduling by assigning jobs based on expertise, location, and urgency. Engineers have real-time access to job details, testing protocols, service history, and compliance requirements via a mobile app, reducing admin time and ensuring calibration and servicing are carried out efficiently.
Yes, engineers can access and update compliance records via a mobile app while on-site. All servicing, testing, and calibration data is logged digitally, ensuring instant updates and reducing paperwork while keeping records audit-ready.
Yes, Service Geeni offers full visibility of medical devices across hospitals, clinics, and laboratories. It allows service teams to remotely monitor asset conditions, calibration schedules, and maintenance history, ensuring all devices remain operational and compliant across multiple locations.
Yes, the software tracks parts inventory and availability, helping service teams ensure that essential components are stocked for maintenance, recalibration, and repairs. Engineers can check part availability in real time, reducing delays and preventing extended downtime for critical medical devices.
Other Industries We Support

Materials Handling & Logistics

Lifting & Access Equipment
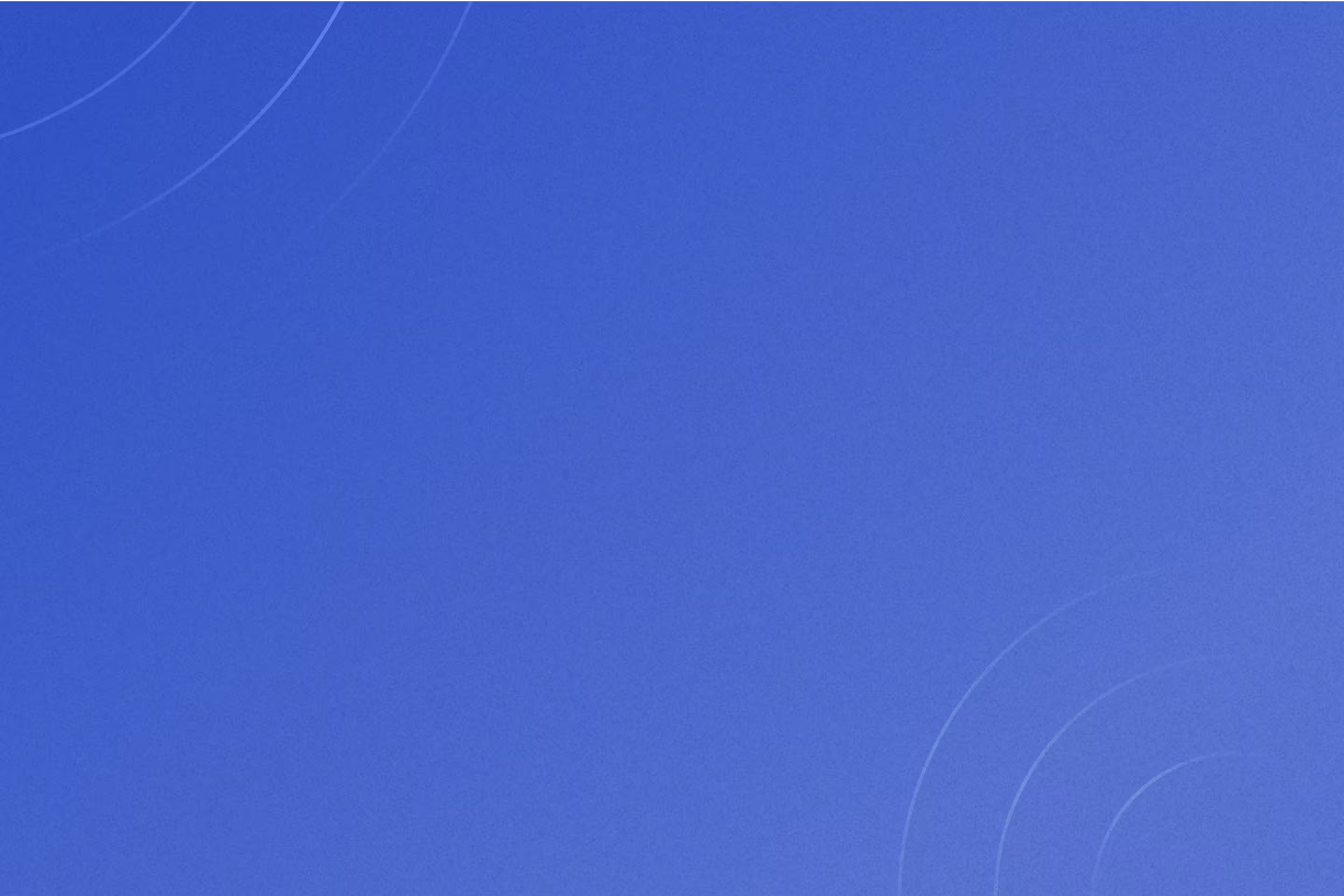
Book Your Demo Today
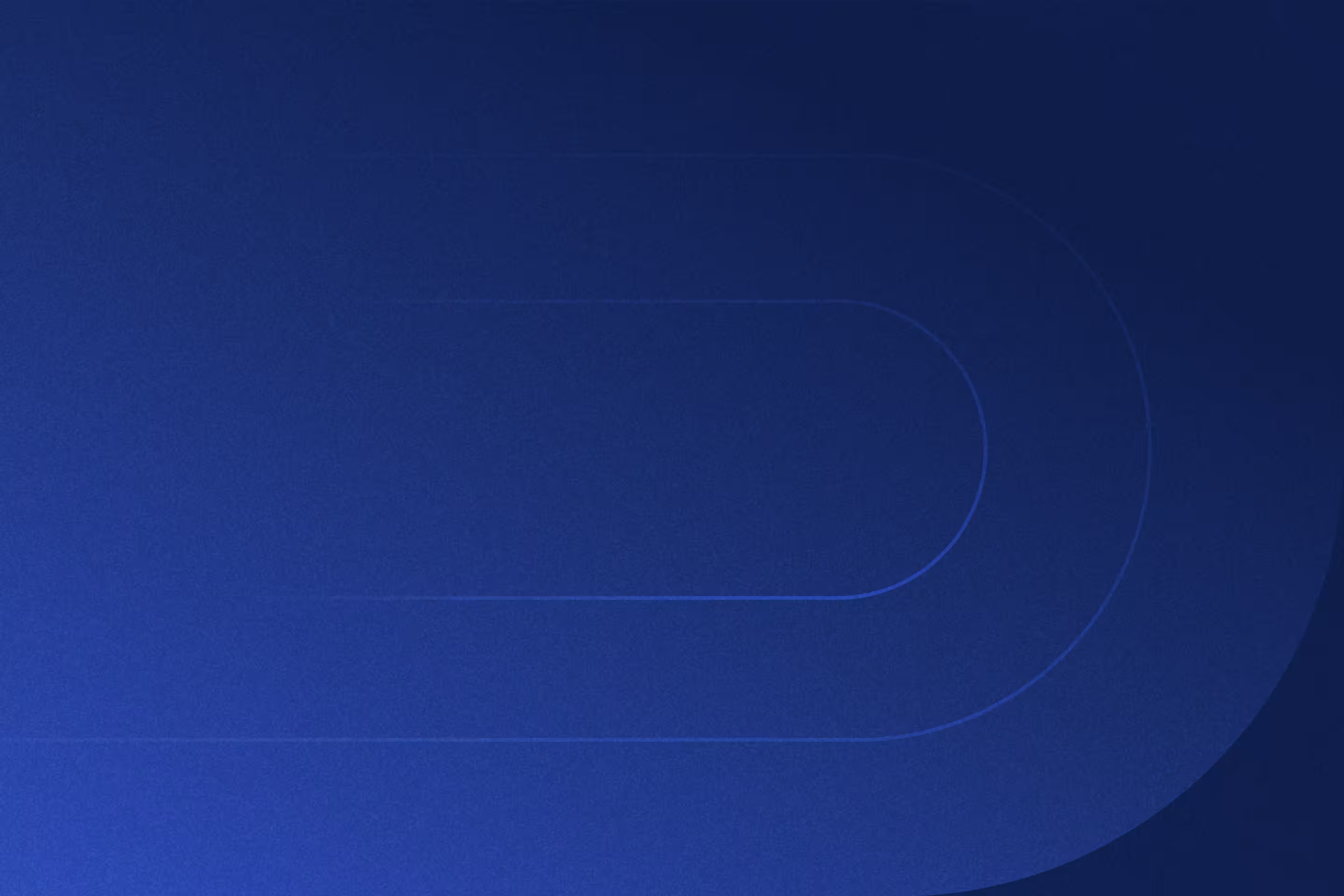